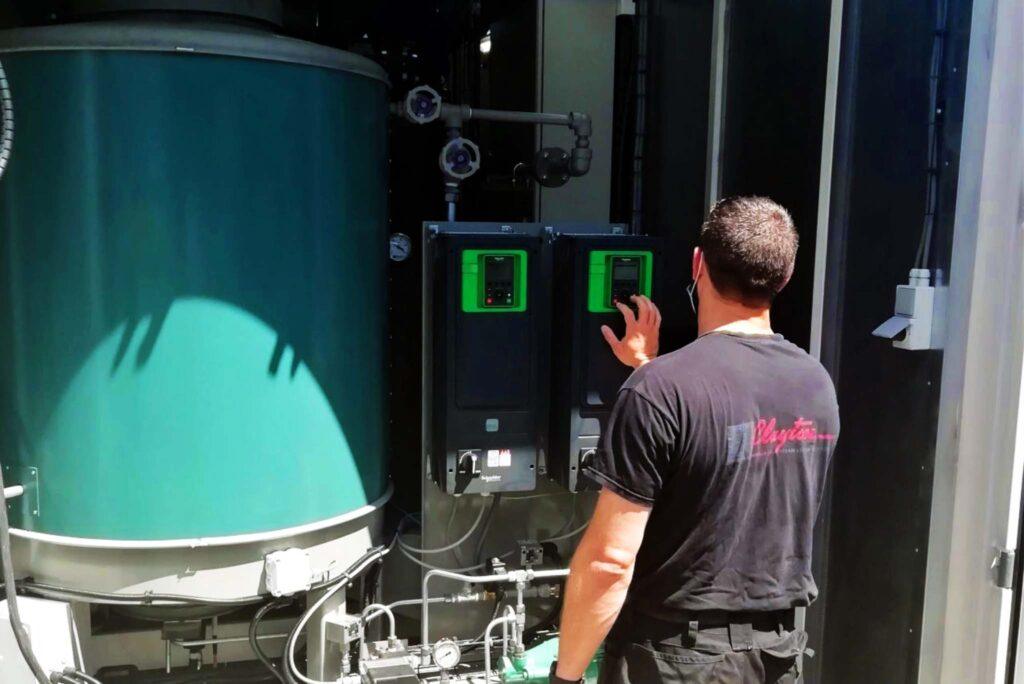
Many companies, refineries, and district-heating plants use industrial steam boiler to generate pressurized vapour for manufacturing. Even the most effective combustion controls waste heat if surrounding surfaces leak thermal energy to ambient air. Effective insulation quietly reduces fuel use, protects staff, and stabilizes operation. Understanding how insulation works and how to maintain it over decades pays off faster than changing burners or adding economisers. It keeps rooms colder, reduces noise, and protects coatings from seasonal weather extremes and unpredictable load patterns’ temperature changes.
Dynamic Boiler Heat Loss
Uninsulated boiler shells radiate and convect 1–3% of their rated output into the boiler room. That lost energy equals thousands of dollars in fuel every month at 10 tons per hour of 10 bar steam. Heat exits via conduction over steel walls, radiation from heated surfaces, and turbulent convection to air. The sharper temperature gradient and more wastage increase with operating pressure.
Key Insulation Materials
Calcium silicate, mineral wool, perlite, and high-temperature aerogel blankets dominate industrial boiler cladding. Calcium silicate is popular for furnace walls because it can endure 1,000 °C and mechanical abuse. Mineral wool retains moisture unless jacketed but is cheaper and easier to shape around elbows. Aerogel composites have the lowest thermal conductivity (below 0.020 W/m·K), allowing engineers to reduce thickness without affecting surface temperature, making them ideal for constrained plant layouts.
Top Insulation Installation Methods
Even premium materials fail if seams gape or supports compress the blanket. To block heat escape, crews must remove rust, prime, and build staggered joints. Stainless-steel bands or sheets secure modules without crushing fibers. For removable doors and inspection ports, hinged coverings with cam locks accelerate access and maintain continuity. Proper installation reduces surface temperatures from 170 to 55 °C, fulfilling OSHA touch restrictions.
Monitoring Performance and Maintenance
Foot traffic, steam leaks, and oil drips damage insulation. Hotspots that burn gasoline but not paint are detected by quarterly infrared scans. A 10 °C rise across identical surfaces generally indicates missing lagging or a moist portion that needs replacement when emissivity settings are correct. Degraded areas spread as moisture wicks, thus facility staff should patch damage within days, not during the following turnaround.
Insulation is a low-risk, high-impact solution that facility managers should not neglect for reducing combustion emissions, protecting staff, or increasing uptime. Every industrial steam boiler performs closer to its design efficiency year after year by paying attention to material selection, installation quality, and repairs.